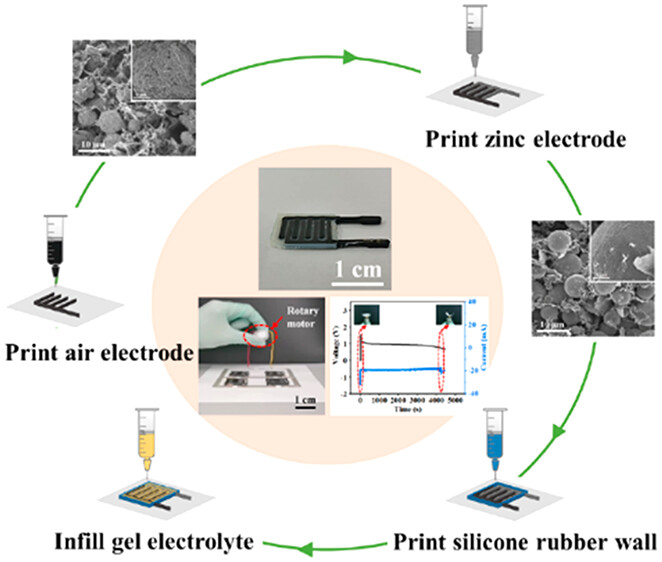
Guoxian Li and Chuizhou Meng’s groups in Mechanical Engineering at the Hebei University of Technology recently published an interesting article pre-print from the American Chemical Society’s Applied Materials & Interfaces. Their research paper shows the simple microfabrication of rechargeable batteries in the form of 3-D printed interdigitated electrodes (IDEs) on a variety of substrates. The appearance and simplified fabrication process of the batteries are illustrated in Figure 1 above right.
The paper and supplementary information provide a fair amount of detail regarding the fabrication process used to make the electrodes. Four slurries were prepared for the air electrode, zinc electrode, interelectrode gel polymer electrolyte, and silicone rubber to close the cell. Figure 2 below left shows the printing process, chemical composition, sizes and examples of the IDE batteries. The air electrode incorporated tricobalt tetraoxide (Co3O4) to catalyse the oxygen reduction during discharge and oxidation (evolution) during charging.
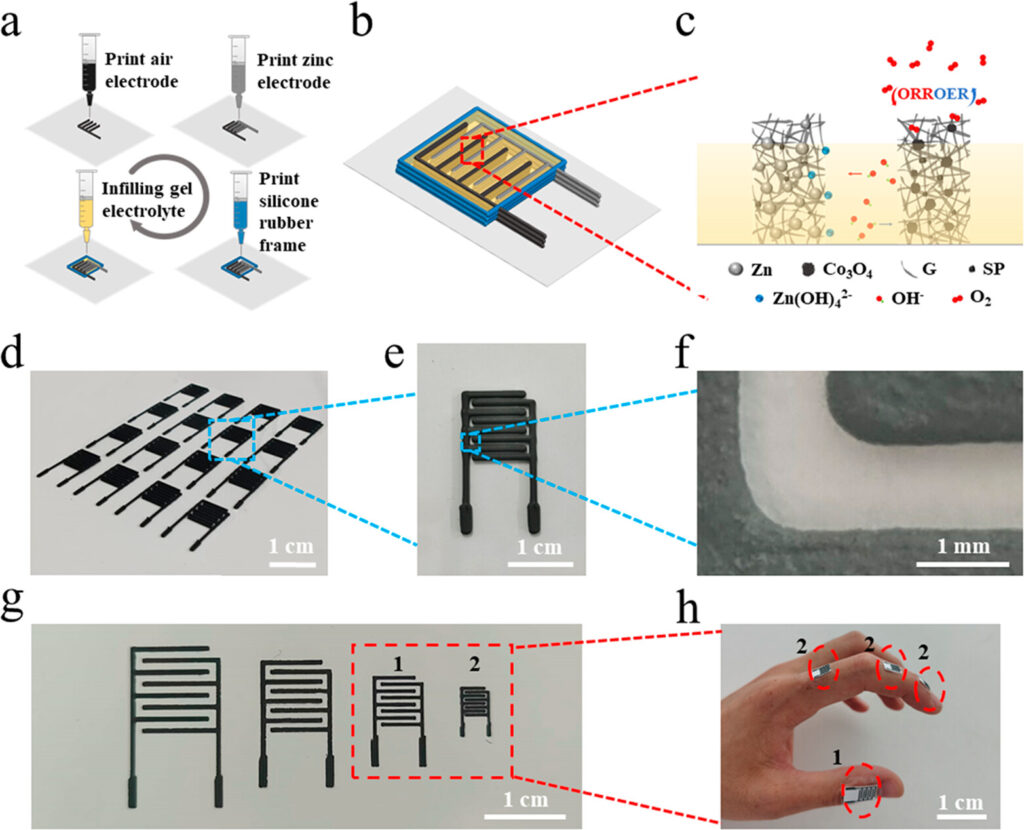
Different sizes (x, y) and thicknesses (z, depending on the number of layers deposited) of IDEs were prepared and characterised; electrode arrays were on the order of 1 cm x 1 cm, with thicknesses on the order of 1.5 mm. Arrangements with batteries in parallel (high current and power), in series (high voltage) or both were evaluated. Figure 3 below shows four batteries arranged in series (a), in parallel (c), and the polarisation & power curves for the single and 4-battery arrangements in each case for series and parallel circuits (b & d, respectively). Open circuit potential (i.e. voltage with no load) of the battery arrangements are also shown in (a) and (c). They claim high power density performance at 77.2 mW•h/cm². Lifetime of full power output varied approximately with the number of layers deposited.
Several examples of printing options and applications were also provided, demonstrating the use of the batteries in powering a fan motor (Figure 3, e-g), LEDs (h-i) and charging a cell phone (j). Interestingly, different Zn/air electrode alignments are possible, as in (h), as are different substrates. Normally, polyethylene terephthalate (PET, a common thermoplastic used for blowmoulding e.g. pop bottles, clamshell produce packages, etc.) in a flat sheet is used, but flexible wristbands (i) and cloth patches (j) were also demonstrated.
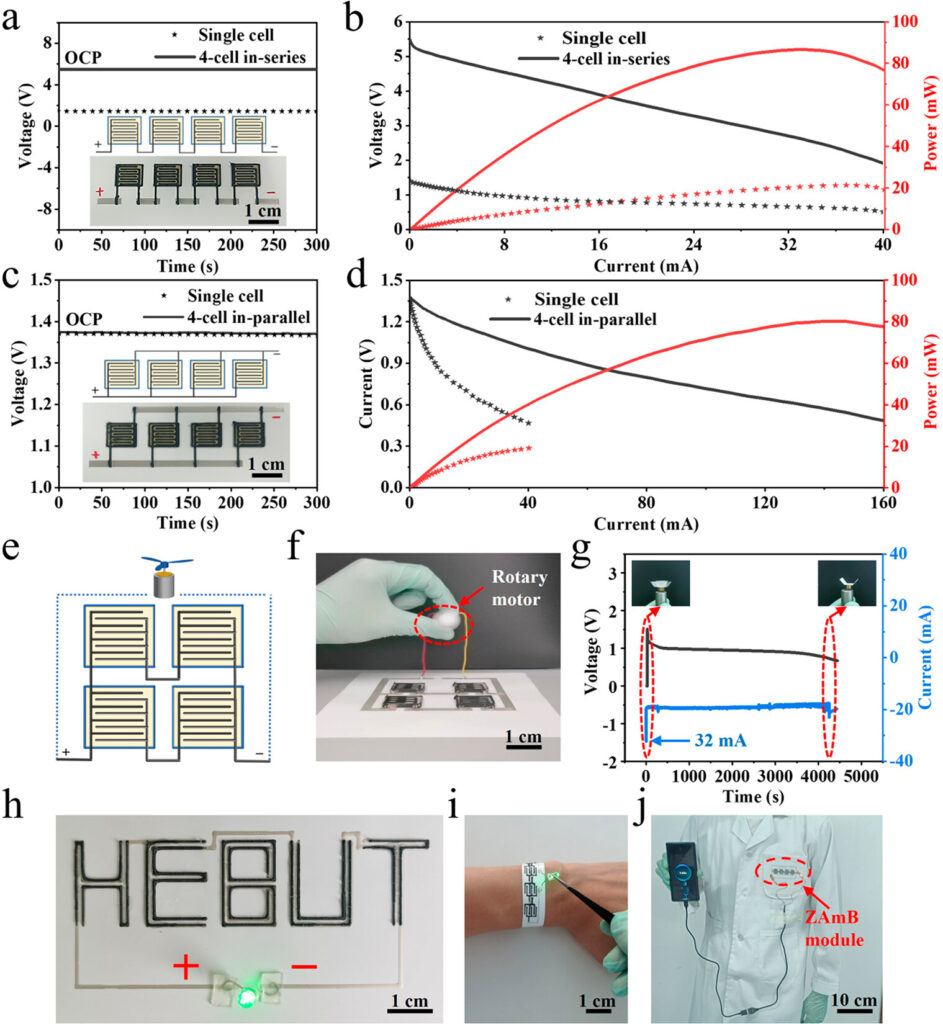
This technology shows significant promise. The use of cobalt oxide as a catalyst and zinc as a metal are important advantages. Compared to the use of expensive noble metals like platinum and ruthenium, the use of Co3O4 as a catalyst is both more economical and environmentally sustainable. Likewise, the authors and others point out that zinc-air batteries have about five times the energy density of lithium-ion batteries, and are a potentially greener alternative. I was also struck by several potential benefits in the context of MEMS and microfluidic devices. The ability to integrate microfabricated batteries to power on-board components, without requiring an additional button cell, presents more opportunities. The battery size (capacity) can be tailored to device needs, reducing costs and waste impact for single-use scenarios. Also, the fact that these batteries are rechargeable opens the door to the development of multi-use or longer use MEMS and microfluidic devices, which can significantly decrease COGS and environmental footprint in an eventual product.